Mass customization can improve the sustainability of fashion — but only under the right conditions.
More than 2,000 pieces of clothing are thrown away every second — amounting to more than 11 million tons of textile waste produced by the fashion industry each year, according to Bloomberg Green. A new study co-authored by a Penn State Smeal College of Business professor suggests that mass customization — the process of having customers order clothing tailored to their own taste and measurements — can be a solution to the fashion industry’s overproduction if adopted under the right circumstances.
Titled “Is Adopting Mass Customization a Path to Environmentally Sustainable Fashion?,” the research paper explores the potential for mass customization (MC) to increase profitability while also reducing the environmental footprint of the fashion industry.
“We draw our motivation largely from the fashion industry, where the modus operandi is mass production of fashion items far in advance of highly uncertain and fickle demand, which typically results in colossal overproduction, and significant contribution to landfills all over the world,” says co-author Aydin Alptekinoğlu, professor of supply chain management, Robert G. Schwartz University Endowed Fellow in Business Administration, and director of research for the Penn State Smeal Center for Supply Chain Research®.

Aydin Alptekinoğlu’s research was inspired by the criticism faced by the fashion industry regarding their harmful environmental impact.
Alptekinoğlu says the research was inspired by the criticism faced by the fashion industry regarding their harmful environmental impact. The goal of the paper is to help further the conversation on how to help the industry transition to a more environmentally friendly future.
In teaching his supply chain management course, Alptekinoğlu says he is used to guiding students in sustainable practices and decision-making. He emphasized that the research embodies Smeal’s emphasis on being socially conscious, stewarding the planet’s resources, and empowering through digital innovation.
“Consumers are increasingly more conscious of the impact of their choices,” Alptekinoğlu says. “This research offers a solution — at a supply chain and operations strategy level — to businesses and proposes policy options to policymakers.”
While mass production relies on a forecast of demand, mass customization is predicated on making things on demand. Some environmentalists have long promoted mass customization as being an effective approach to improving sustainability within the fashion industry. In contrast, the paper suggests that this can be true in some conducive market conditions, but it also reveals that mass customization could cause overproduction and harm the environment.
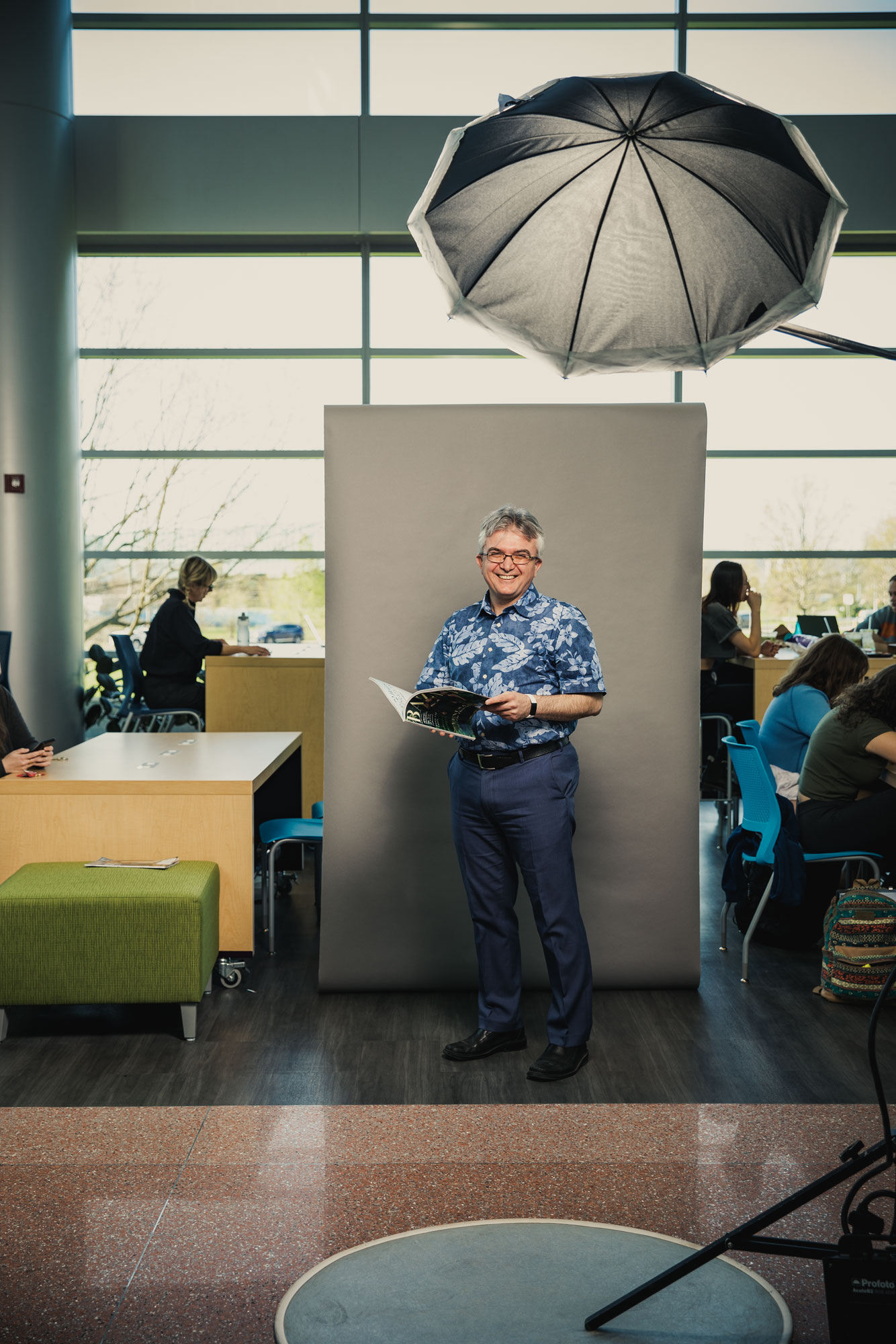
“We found that making the wait for bespoke fashion more acceptable or tolerable for consumers expands the potential of mass customization to generate win-win opportunities in fashion.”
Alptekinoğlu and co-author Adem Orsdemir, a professor of operations and supply chain management at the University of California Riverside, studied three policy ideas to understand whether they could expand mass customization’s ability to generate a positive environmental response: promoting it and making it more acceptable to wait for customizable products to be made, charging a disposal fee for overproduction, and recycling excess inventory and used items.
“We found that making the wait for bespoke fashion more acceptable or tolerable for consumers expands the potential of mass customization to generate win-win opportunities in fashion,” Alptekinoğlu says.
For example, Alptekinoğlu says that the researchers theorized that luxury fashion is “ripe for sustainable MC adoption” due to higher product values.
He said he hopes the paper will be able to impact industry practice and policymaking. Additionally, Alptekinoğlu said he wants to use the research as a springboard for reaching out to Smeal alumni who are in positions to make a difference in the fashion industry.
The paper is set to be published in Manufacturing & Service Operations Management, a top journal that covers research about operations and supply chain management, later this year.